業務改善を進めるために役に立つ手法
~製造業の手法を応用して効率的に進める~
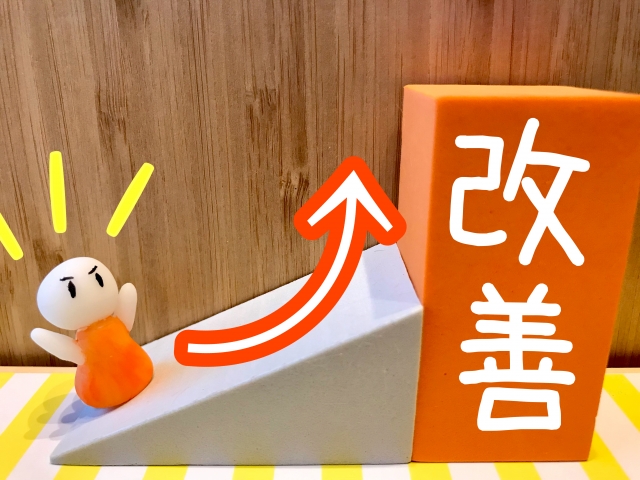
業種にかかわらず、生産や販売といった企業活動を行うなかで、さまざまな問題点が生じ、解決が必要になる場面が多くあります。問題点を把握して改善策を検討するにあたり、作業や時間の面でなるべくムリ・ムダ・ムラを省き効率的に行うほうがよいはずです。
そのために活用できる手法がいくつかあります。おもに製造業の生産現場で用いられる手法ですが、ほかの業種にも応用できます。
①5W2H
5W2Hの視点から現状把握し改善案を検討するものです。
㋐What:何を行っているのか(内容)
→【改善の視点】作業内容は適切か、ほかにやるべきことはないか
㋑Why:なぜ行っているのか(目的)
→【改善の視点】作業の必要性はあるか、なくせないか
㋒When:いつ行っているのか(時期)
→【改善の視点】最適な時期はいつか、順番は適切か
㋓Who:だれが行っているのか(作業者)
→【改善の視点】だれが適任者か、メンバーや分担は適切か
㋔Where:どこで行っているのか(場所)
→【改善の視点】もっとよい場所はないか
㋕How to:どのように行っているのか(方法)
→【改善の視点】もっとよい方法はないか
㋖How much:いくらで行っているのか(原価)
→【改善の視点】もっと安くできないか
②ECRS原則
「工程、作業、動作を対象とした分析に対する改善の指針として用いられる、E(eliminate:なくせないか)、C(combine:一緒にできないか)、R(rearrange:順序の変更はできないか)、S(simplify:単純化できないか)による問いかけ」(JIS Z 8141-5305)です。
㋐Eliminate(排除)
まず、必要のないものをなくすことを検討します。
㋑Combine(結合と分離)
次に、類似のものを結合することと、異質なものを分離することを検討します。
㋒Rearrange(入替えと代替)
次に、順序や場所、担当者などの入替えや代替を検討します。
㋓Simplify(簡素化)
最後に、自動化や単純化などを検討します。
③3S
「標準化、単純化、専門化の総称であり、企業活動を効率的に行うための考え方」(JIS Z 8141-1105)です。
㋐単純化(Simplification)
取扱製品・商品や作業手順、システムなどは複雑すぎるとわかりにくく、作業しにくくなります。複雑さを減らすことで効率化を図ります。
㋑標準化(Standardization)
共通部品を使ったり、作業内容や管理手法などを整理統一したりすることで効率化を図ります。部品を規格化することや、マニュアルの作成などにより何が標準なのかを明文化することも一例です。
㋒専門化(Specialization)
専任担当者を配置したり、多角化でなく専業化したりすることで、特定の機能に特化して効率化を図るものです。
④5S
職場環境の維持改善のために行う活動です。
㋐整理
いるものといらないものを分別し、いらないものを捨てることです。
㋑整頓
決められた物を決められた場所に置き、だれでもわかるようにして、いつでも取り出せる状態にしておくことです。
㋒清掃
常に掃除をしてきれいにしておくことです。
㋓清潔
3S(㋐整理・㋑整頓・㋒清掃)を維持し職場の衛生を保つことです。
㋔躾
決められたルール・手順を正しく守る習慣をつけることです。
⑤動作経済の原則
「作業者が作業を行うとき、最も合理的に作業を行うために適用される経験則」(JIS Z 8141-5207)です。
㋐動作の数を減らす
㋑動作を同時に行う
㋒動作の距離を短くする
㋓動作を楽にする
上記の4つの原則を、3つの場面(身体の使用、作業場の配置、設備・工具の設計)に照らし合わせて効率化を検討するものです。たとえば、作業の無駄な動きをなくしたり、作業動線が最短になるようにしたり、作業しやすくなるよう設備を設計・配置したりといったことです。
⑥目で見る管理
「作業者又は管理者が、進捗状況又は正常か異常かどうかといった生産の状況を一目で見て分かり、管理しやすくした工夫」(JIS Z 8141-4303)です。いわゆる「見える化」です。
現場ではさまざまな問題が発生します。異常事態や問題の発生を出来るだけ早く把握して現場のメンバー全員で共有することで問題が大きくなることを防ぐ必要があります。そのために、次のような、視覚で確認できるツールを設置しておくというものです。
㋐アンドン
工場で工程に異常が発生したとき、赤色点灯するなどして工場内に周知する表示灯。
㋑標準作業票又は作業限界線(定位置停止線)
人や設備、物を効率的に作業できるよう標準的な作業方法を取り決め、それを記載して作業場に提示するもの。作業が決められた通り行われているかチェックできる。
㋒生産管理板、在庫表示板
工場の各部署における生産状況や在庫状況などを記入して表示して管理できるようにするもの。
製造業以外でも、不用品に赤札をつけて区別するとか、業務終了時刻にチャイムを鳴らして無駄な残業をけん制するとか、さまざまな方法が考えられます。
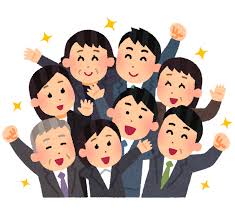
ほかにもさまざまな業務改善の手法があります。自社で使えそうな手法を取り入れたり参考にしたりして、業務改善自体も効率よく行うことをおすすめします。